Monday, December 24, 2018
Monday, December 17, 2018
Wednesday, December 12, 2018
Monday, December 10, 2018
Wednesday, November 28, 2018
Tuesday, October 30, 2018
Industry 4.0
Industry 4.0 is a name given to the current trend of automation and data exchange in manufacturing technologies. It includes cyber-physical systems, the Internet of things, cloud computing and cognitive computing. Industry 4.0 is commonly referred to as the fourth industrial revolution.
Industry 4.0 fosters what has been called a "smart factory". Within modular structured smart factories, cyber-physical systems monitor physical processes, create a virtual copy of the physical world and make decentralized decisions. Over the Internet of Things, cyber-physical systems communicate and cooperate with each other and with humans in real-time both internally and across organizational services offered and used by participants of the value chain.
Name
The term "Industry 4.0", sometimes shortened to I4.0 or simply I4, originates from a project in the high-tech strategy of the German government, which promotes the computerization of manufacturing.[6]
The term "Industry 4.0" was revived in 2011 at the Hangover Fair. In October 2012 the Working Group on Industry 4.0 presented a set of Industry 4.0 implementation recommendations to the German federal government. The Industry 4.0 work group members are recognized as the founding fathers and driving force behind Industry 4.0.
On 8 April 2013 at the Hangover Fair, the final report of the Working Group Industry 4.0 was presented.[8]. This working group was headed by Siegfried Dais (Robert Bosch GmbH) and Henning Kagermann (German Academy of Science and Engineering).
As Industry 4.0 principles have been applied by companies they have sometimes been re-branded, for example the aerospace parts manufacturer Meggitt PLC has branded its own Industry 4.0 research project M4.
Design principles
There are four design principles in Industry 4.0. These principles support companies in identifying and implementing Industry 4.0 scenarios.
- Interconnection: The ability of machines, devices, sensors, and people to connect and communicate with each other via the Internet of Things (IT) or the Internet of People
- Information transparency: The transparency afforded by Industry 4.0 technology provides operators with vast amounts of useful information needed to make appropriate decisions. Inter-connectivity allows operators to collect immense amounts of data and information from all points in the manufacturing process, thus aiding functionality and identifying key areas that can benefit from innovation and improvement.[11]
- Technical assistance: First, the ability of assistance systems to support humans by aggregating and visualizing information comprehensively for making informed decisions and solving urgent problems on short notice. Second, the ability of cyber physical systems to physically support humans by conducting a range of tasks that are unpleasant, too exhausting, or unsafe for their human co-workers.
- Decentralized decisions: The ability of cyber physical systems to make decisions on their own and to perform their tasks as autonomously as possible. Only in the case of exceptions, interference's, or conflicting goals, are tasks delegated to a higher level.
Meaning
Current usage of the term has been criticized as essentially meaningless, in particular on the grounds that technological innovation is continuous and the concept of a "revolution" in technology innovation is based on a lack of knowledge of the details.
The characteristics given for the German government's Industry 4.0 strategy are: the strong customization of products under the conditions of highly flexible (mass-) production. The required automation technology is improved by the introduction of methods of self-optimization, self-configuration, self-diagnosis, cognition and intelligent support of workers in their increasingly complex work The largest project in Industry 4.0 as of July 2013 is the BMBF leading-edge cluster "Intelligent Technical Systems Ostwestfalen-Lippe (it's OWL)". Another major project is the BMBF project RES-COM,[15] as well as the Cluster of Excellence "Integrative Production Technology for High-Wage Countries" In 2015, the European Commission started the international Horizon 2020 research project CREMA] (Providing Cloud-based Rapid Elastic Manufacturing based on the XaaS and Cloud model) as a major initiative to foster the Industry 4.0 topic.
Effects
In June 2013, consultancy firm McKinsey released an interview featuring an expert discussion between executives at Robert Bosch - Siegfried Dais (Partner of the Robert Bosch Industrietreuhand KG) and Heinz Derenbach (CEO of Bosch Software Innovations GmbH) - and McKinsey experts. This interview addressed the prevalence of the Internet of Things in manufacturing and the consequent technology-driven changes which promise to trigger a new industrial revolution. At Bosch, and generally in Germany, this phenomenon is referred to as Industry 4.0. The basic principle of Industry 4.0 is that by connecting machines, work pieces and systems, businesses are creating intelligent networks along the entire value chain that can control each other autonomously.
Some examples for Industry 4.0 are machines which can predict failures and trigger maintenance processes autonomously or self-organized logistics which react to unexpected changes in production.
According to Dais, "it is highly likely that the world of production will become more and more networked until everything is interlinked with everything else". While this sounds like a fair assumption and the driving force behind the Internet of Things, it also means that the complexity of production and supplier networks will grow enormously. Networks and processes have so far been limited to one factory. But in an Industry 4.0 scenario, these boundaries of individual factories will most likely no longer exist. Instead, they will be lifted in order to interconnect multiple factories or even geographical regions.
There are differences between a typical traditional factory and an Industry 4.0 factory. In the current industry environment, providing high-end quality service or product with the least cost is the key to success and industrial factories are trying to achieve as much performance as possible to increase their profit as well as their reputation. In this way, various data sources are available to provide worthwhile information about different aspects of the factory. In this stage, the utilization of data for understanding current operating conditions and detecting faults and failures is an important topic to research. e.g. in production, there are various commercial tools available to provide overall equipment effectiveness (OEE) information to factory management in order to highlight the root causes of problems and possible faults in the system. In contrast, in an Industry 4.0 factory, in addition to condition monitoring and fault diagnosis, components and systems are able to gain self-awareness and self-productiveness, which will provide management with more insight on the status of the factory. Furthermore, peer-to-peer comparison and fusion of health information from various components provides a precise health prediction in component and system levels and force factory management to trigger required maintenance at the best possible time to reach just-in-time maintenance and gain near-zero downtime.[19]
During EDP Open Innovation conducted in Oct 2018 at Lisbon, Portugal, Industry 4.0 conceptualization was extended by Sens-fix B.V. a Dutch company with introduction of M2S terminology. It essentially is characterizing upcoming service industry to cater to millions of machines, managed by the machines themselves, fortunately using Artificial intelligence developed by humans!.
Challenges
Challenges in implementation of Industry 4.0:
- IT security issues, which are greatly aggravated by the inherent need to open up those previously closed production shops
- Reliability and stability needed for critical machine-to-machine communication (M2M), including very short and stable latency times
- Need to maintain the integrity of production processes
- Need to avoid any IT snags, as those would cause expensive production outages
- Need to protect industrial know how (contained also in the control files for the industrial automation gear)
- Lack of adequate skill-sets to expedite the march towards fourth industrial revolution
- Threat of redundancy of the corporate IT department
- General reluctance to change by stakeholders
- Loss of many jobs to automatic processes and IT-controlled processes, especially for lower educated parts of society
- Low top management commitment
- Unclear legal issues and data security
- Unclear economic benefits/ Excessive investment
- Lack of regulation, standard and forms of certifications
- Insufficient qualification of employees
Role of big data and analytics
Modern information and communication technologies like cyber-physical system, big data analytics and cloud computing, will help early detection of defects and production failures, thus enabling their prevention and increasing productivity, quality, and agility benefits that have significant competitive value.
Big data analytics consists of 6 Cs in the integrated Industry 4.0 and cyber physical systems environment. The 6C system comprises:
- Connection (sensor and networks)
- Cloud (computing and data on demand)
- Cyber (model & memory)
- Content/context (meaning and correlation)
- Community (sharing & collaboration)
- Customization (professionalization and value)
In this scenario and in order to provide useful insight to the factory management, data has to be processed with advanced tools (analytics and algorithms) to generate meaningful information. Considering the presence of visible and invisible issues in an industrial factory, the information generation algorithm has to be capable of detecting and addressing invisible issues such as machine degradation, component wear, etc. in the factory floor.
Impact of Industry 4.0
Proponents of the term claim Industry 4.0 will affect many areas, most notably:
- Services and business models
- Reliability and continuous productivity
- IT security: Companies like Symantec, Cisco, and Penna Security have already begun to address the issue of security
- Machine safety
- Manufacturing Sales: Companies like Logic-bay Corporation have released multiple resources addressing Industry 4.0 in the manufacturing sales channel.
- Product life cycles
- Industry value chain
- Workers' education and skills
- Socio-economic factors
- Industry Demonstration: To help industry understand the impact of Industry 4.0, Cincinnati Mayor John Cranley, signed a proclamation to state "Cincinnati to be Industry 4.0 Demonstration City".
- An article published in February 2016 suggests that Industry 4.0 may have a beneficial effects for emerging economies such as India.[24]
The aerospace industry has sometimes been characterized as "too low volume for extensive automation" however Industry 4.0 principles have been investigated by several aerospace companies, technologies have been developed to improve productivity where the upfront cost of automation cannot be justified, one example of this is the aerospace parts manufacturer Meggitt PLC's project, M4. The discussion of how the shift to Industry 4.0, especially digitization, will affect the labor market is being discussed in Germany under the topic of Work 4.0.
https://en.wikipedia.org/wiki/Industry_4.0
LEOPAD CHALLENGE TROPHY 2018
DATE : 24TH NOVEMBER 2018
TIME : 7.30 A.M - 6.00 P.M
VENUE : LAVANA SPORTS, JALAN GENTING KELANG,TAMAN DANAU KOTA,
51300, KUALA LUMPUR.
EXCITING CASH PRIZES
i)WINNER OF THE CATEGORY
(men's doubles & women's doubles)
GOLD MEDAL / HEAD
CASH PRIZE RM2000 / PAIR
HAMPER / PAIR
ii)1st RUNNER UP OF THE CATEGORY
(men's doubles & women's doubles)
SILVER MEDAL / HEAD
CASH PRIZE RM1000 / PAIR
HAMPER / PAIR
iii) 2nd RUNNER UP OF THE CATEGORY
(men's doubles & womens doubles)
BRONZE MEDAL / HEAD
CASH PRIZE RM500 / PAIR
HAMPER / PAIR
IV) OVERALL CHAMPIONSHIP WINNER
(winning team will be awarded based on point system)
CHAMPIONSHIP TROPHY
V) LUCKY DRAW PRIZES FOR 15 INDIVIDUALS
(open to participants and volunteers ONLY)
GRAND PRIZE
SECOND PRIZE
THIRD PRIZE
4th - 15th PRIZE
Wednesday, September 12, 2018
SafetyWorks! Tool Box Talks
SafetyWorks! Tool Box Talks cover a variety of common workplace safety and health problems. Read them, post them, share them with others, or use them for safety meetings.
Tool Box Talks
Proper Lifting I Using Hammers and Chisels I Compressed Gas I The Deadly Dozen I Electrical Hazards I Excavations I Eye Protection I Fire Protection and Control I Guardrails I Head Protection - Hard Hats I Heat Exhaustion / Sunstroke I Heavy Equipment Hazards I Heavy Equipment I Ladder Safety I Power Lines and Mobile Cranes I Clothing (PPE) I Personal Protective Equipment - Concrete Construction I Safety Training Steps I Traffic Control I Mobile Scaffold Safety ITurn a Safety Works! Tool Box Talk into a Safety Meeting
A safety meeting -- or toolbox talk -- is an opportunity to discuss a specific safety and health topic in an informal setting. It's intended to be participatory, encouraging questions and discussion and drawing on workers' experience. It's not a lecture and there are no tests.
The safety meeting can be short (10-20 minutes) and it can be part of an existing staff or crew meeting.
Before you being the meeting:
- Does this topic relate to your workplace? If not, choose another topic.
- Look up your company rules or policies about this topic.
- Find out about any injuries, accidents or close calls in your company related to this topic.
- Do not hand out copies of the Safety Tip until after the meeting. You want workers to contribute their own ideas, not read off the sheet.
Begin the meeting:
- Read Section I to everyone at the meeting.
- Ask if anyone has a personal story about this topic. Or add one of your own. Get people involved. The meeting will work best if everyone participates.
- Ask the question in Section II. Give people time to suggest possible answers. Add points that no one mentions from the answers in Tips Section II.
- Discuss any problems at your workplace related to this topic. Ask: “Do you know of any problems with (this topic) at this workplace?” This might be a good time to bring up the injuries, accidents or close calls you found out about. Invite questions --- Remind people that there's no such thing as a stupid question.
- Ask the question in Section III. Again, give people time to suggest possible answers. Add points that no one mentions from the answers in the Tips Section III. Ask: "What can we do to solve our problems with (this topic)?" Encourage discussion.
- Ask: “Have you had any experience with (this topic) here or at other places you’ve worked that might help us work safer here?”
- If the company has rules or procedures around this topic, discuss them now.
- Ask if there’s anything else anyone wants to mention on this topic. Stick to the topic. If questions and comments stray from the meeting topic, tell people their questions will be addressed later, either privately or at a future safety meeting.
- Before you close, remind workers how to report any safety problems at your workplace.
After the meeting:
If you want, hand out copies of the Tool Box Talk sheet or post a copy on the bulletin board.
If anyone want to know more about this topic, try the OSHA web page or use the SafetyWorks! Ask the Expert page.
Email SafetyWorks! to suggest a topic for a future SafetyWorks! Tool Box Talk.
Tuesday, September 11, 2018
WORKPLACE SAFETY TIPS
A COMPREHENSIVE RESOURCE
"Protect your hands; you need them to pick up your pay check." And that may very well be the case, but that’s only the beginning. To ensure that you don’t become an afterthought, make safety your first thought with these workplace safety tips.
GENERAL PRECAUTIONS
Your safety is your personal responsibility.
Always follow the correct procedures.
Never take shortcuts.
Take responsibility and clean up if you made a mess.
Clean and organize your workspace.
Ensure a clear and easy route to emergency exits and equipment.
Be alert and awake on the job.
Be attentive at all times to your work surroundings.
When in doubt, contact your supervisor or manager for instruction, guidance, or training.
Never take risks when it comes to safety.
Obey safety signs, stickers, and tags.
Take short breaks when you keep up a repetitive motion for a long period of time, and sit, stand, or walk with good posture.
Report serious injuries immediately to a supervisor and get emergency assistance.
Keep things in perspective. Hazards may be limitless, so focus on the most likely risks first.
- Strained backs and sliced fingers may be more popular in your workspace than would the risk of flooding (as in a basement office) or the risk of wild animals cutting loose (as in a zoo).
SAFETY IS A TEAM EFFORT
Educate everyone in the workplace about the safety requirements and consider posting a list of workplace safety tips. A workplace safety training will help them reduce or eliminate injuries and illnesses from occurring in the workplace.
Always keep the communication lines open with your co-workers, employers, or employees in order to promote and maintain a safe environment.
Immediately notify others of any (new or old) hazards that you perceive.
Be alert to hazards that could affect anyone— not just yourself; in this respect, maintain a team mentality at all times.
Report a hazardous condition immediately to your manager or supervisor.
Be conscious as to what others are doing around you, and do your best to ensure you don’t pose a hazard to them (and vice versa).
If you’re an employer, invite and involve your employees in safety planning; obtain their insight, give and take suggestions, and ensure that everyone is on the same page.

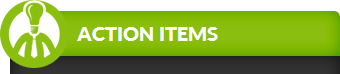
- Always be awake and alert in your workspace.
- Immediately clean and/or report any potential hazards (spills, leaks, fire hazard obstacles)
- Closely follow instructions when using any tool or machine.
- Dress appropriately for your specific workspace and/or task.
- Always wear the protective equipment that is intended for your task.
- Make safety your first thought—not your afterthought!
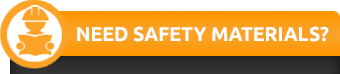
- Over 10,000 Safety Videos
- Topics Covering All Industries
- DVDs, Online and Interactive Options
- Training as low as $89
AN UPLIFTING THOUGHT: LIFTING AND CLIMBING SAFELY
Always use both hands when lifting a heavy or cumbersome object.
Adopt a proper stance for lifting: put the strain on your legs, not your back (crouch at your feet, keep your back straight, and don’t bend at the waist).
Test the weight before you lift something up completely; it might be too late if you realize a few seconds later that it’s too heavy or cumbersome for you.
- An easy way to do this is to nudge it with your foot first.
Consider a back brace if the work is heavy or you have a sensitive back.
Move your feet, not your back, when you want to travel or turn while carrying a heavy load.
Lift slowly and smoothly.
Keep your burden close to your body; this means less strain on you.
If your load is too heavy for you to handle alone, don’t be shy—ask for help!
Ensure ladders are secure and steady before climbing aboard.
Never climb on improvised ladders. Shelves and storage units are poor substitutes. Don’t be lazy, and find a proper solid ladder.
Don’t let appearances fool you. Railings might appear solid and fixed, but they might be improperly secures; at least, test them first.
Use safety harnesses if your job includes heights.
Eliminate distractions when working on a roof, scaffold, or other elevated platform. More than ever, stay focused and alert!
Keep an eye out on the floor to ensure it’s free of obstacles and spills. If it isn’t, get cleaning!
TOOLS AND MACHINERY: PUTTING SAFETY FIRST
Use machinery only if you’re authorized, trained, and alert.
Always use the appropriate tool for the respective task.
Clean your tools and keep them in good working order.
Organize your tools and don’t be careless; someone could easily slip or get hit due to a misplaced object.
Always ensure that the operator of a machine sees you; never approach from behind or from a blind side.
Do not perform a task unless you’ve been trained and you are aware of the hazards as well as how to mitigate/eliminate them.
Never leave machinery running unattended.
Never remove safety guards that are in place to protect you and the surrounding area.
Obey all operating instructions.
If something is wrong, stop the machine immediately and get assistance.
Communicate your location and process to those around you, so they’ll know where you are, what you’re doing, and when they need to be getting out of the way.
Never walk in front of a forklift, tractor, or any other heavy machine; the operator may not have seen you—and, even if he has, there’s always room for error, so make sure that error isn’t you being trampled.
Always read labels and instructions alerting you to potential dangers and hazards.
Unless it’s your job, never tamper with electric controls, cords, switches, or other such hazardous items.
Dress properly and compactly: billowing, loose, or hanging clothes and accessories (ties, earrings, bracelets, loose sleeves, etc.) may easily get caught up in moving parts.
- At best, the offending objects may be destroyed; at worst, they could ruin the machine or severely hurt you.
Never insert fingers or any other objects that don’t belong into moving machinery.
Turn off machines and equipment before you even consider cleaning, un-jamming, oiling, adjusting, or moving them.
BEWARE OF FIRE HAZARDS
Come up with a fire emergency plan; ensure that everyone knows and understands it.
Practice fire drills.
Avoid “power strips” which can ignite a fire if overloaded.
Ventilation is critical, especially if dealing with fumes and chemicals.
- Good ventilation helps to reduce the toxins in the air, and thus to eliminate highly flammable vapors.
In case of fire, know what has fed the fire.
- Never fight a grease fire with water; water will splash the oil and spread the flames.
- Be aware of the whereabouts and use of fire extinguishers.
GEARING UP FOR SAFETY
Always wear appropriate clothing and shoes respective to your job.
Fire extinguishers must be available and readily attainable.
First aid kits must be available and readily attainable.
Never remove or tamper with safety devices.
Use a back brace if you’re lifting heavy objects or you’ve got a sensitive back.
A hard hat will protect you if there’s a risk of falling objects
Wear gloves if you’re handling sharp objects or toxic substances.
Wear goggles if your work poses a hazard to your eyes.
Wear safety harnesses if you’re working from an elevated location and there’s the risk of falling.
Wear non-skid footgear:
- If your workspace involves slippery surfaces (kitchens, spas, pools, etc.)
- If you’re lifting heavy items
Wear a breathing mask at all times, especially if:
- You deal with dangerous or toxic chemicals or fumes
- Your workspace has poor ventilation
- Your workspace has debris, dust, and other flying particles.
Wear the protective equipment that is intended and recommended for your particular task.
- Seat belts
- Safety glasses or goggles
- Protective clothing, headgear, and/or footgear
- Safety harnesses, etc.
Subscribe to:
Posts (Atom)
Happy Deepavali
The festival of light is here! May you be the happiest and may love be always with you. Happy Deepavali!

-
The first practical use of cathodic protection is generally credited to Sir Humphrey Davy in the 1820s. Davy’s advice was sought by the Roy...